Tip of the Month: For Shock Calibration - Avoid 1/4-28 Studs with Large Shoulders
|
For shock calibration, avoid �-28 studs with large shoulders. They do not recess into the reference sensor's counter bore and will cause artificially low calibration results at high amplitudes.
|
Technical Exchanges
|
February 2-5, 2015
Orlando, FL
NCSLI Technical Exchange Half-Day Seminar
The Modal Shop, Inc.
8 am - 12 pm
February 12, 2015
Raleigh, NC
The Modal Shop, Inc.
10 am - 3 pm
March 3, 2015
Los Angeles/Torrance, CA
The Modal Shop, Inc.
10 am - 3 pm
March 5, 2015
San Jose, CA
March 18-20, 2015
Anaheim, CA
|
Quick Links
|
ISO TC 108 - Mechanical vibration, shock and condition monitoring
ISO TC 108/SC 3 - Use and calibration of vibration and shock measuring instruments
|
Previous Newsletters
|
Why the Word 'Hermetic' is Important to Your Piezoelectric Sensors; FAQ: When an Accelerometer Fails Calibration
Know Your Standard: ISO 16063; University of Buffalo Calibrates Seismic Sensors for Earthquake Simulation
|
Select Newsletter Articles
by Topic
|
|
|
|
How Does Test Level Affect Sensitivity?
By Patrick Timmons Dynamic Calibration Systems Engineer
|
In this month's article we are going to explore an often overlooked sensor specification: amplitude linearity. Linearity, defined quite simply, is a numerical value that expresses how much a sensor's sensitivity changes with respect to the change in excitation amplitude. Linearity tests are commonly conducted for sensors with a relatively "low" sensitivity because these sensors generally experience more extreme measurement conditions. In the sound and vibration world, these are the sensors that are often used to capture high-energy events such as shock events for acceleration, and blast events for pressure. Due to the high variability in excitation that these sensors undergo, test and measurement engineers will often specify to continually quantify the performance of a sensor's linearity during its recalibration cycle to ensure consistent results...
modalshop.com/calibration.asp?ID=1024
|
Calibrating Bently Nevada� Velomitors� with ICP� Signal Conditioning
By Mike Scott Portable Vibration Calibration Product Manager
|
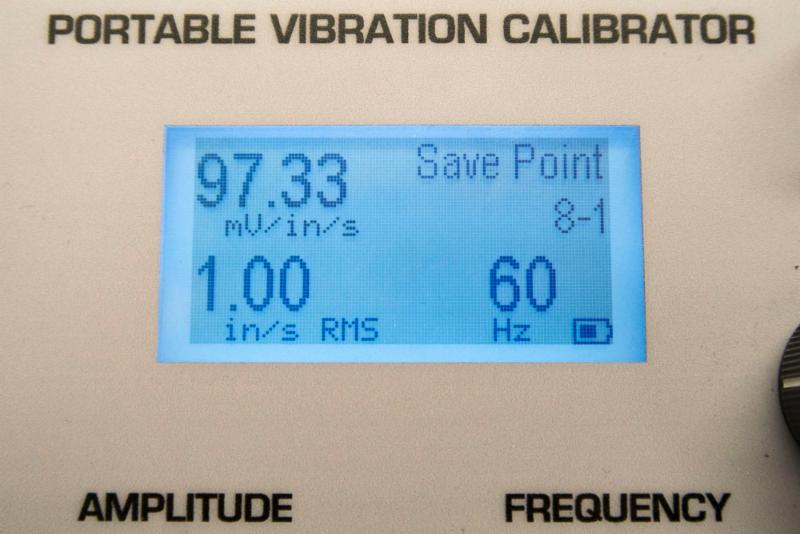 Bently Nevada� - a wholly owned subsidiary of General Electric Company - has been a trusted partner for power generation and petrochemical companies in the field of machinery protection and condition monitoring for more than 50 years. An extensive line of velocity sensors and accelerometers pairs with non-contact proximity probes to help customers keep critical equipment like gas and steam turbines running. The company's series of Velomitors� are similar in appearance to industrial ICP� accelerometers and feature the same 100 mV/inch per second (3.94 mV/mm/second) output as many ICP� velocity output designs. But their -24 VDC power requirement and two-wire design can be challenging for...
|
Blast from the Past: Introduction to Industrial Accelerometers
|
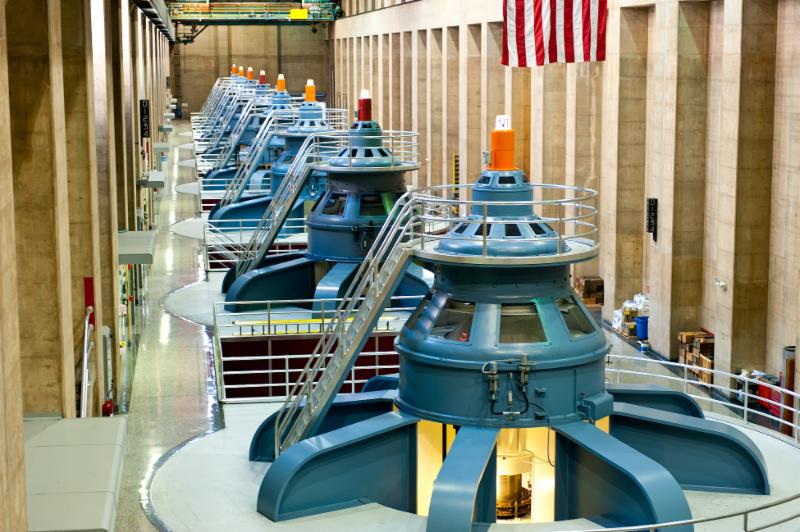 The basics of acceleration sensing for the plant floor come from the same measurement/laboratory grade instruments we have been using for years. However, the packaging of industrial accelerometers differs significantly from their laboratory style heritage. At the core of an industrial style accelerometer is still a piezoelectric crystal. Piezoelectric (PE) accelerometers have become the defacto standard for machinery and process vibration for a number of reasons...
|
|
Thanks for joining us for another issue of "Dynamic Sensors & Calibration Tips". As always, please speak up and let us know what you like. We appreciate all feedback: positive, critical or otherwise. Take care!
Sincerely,
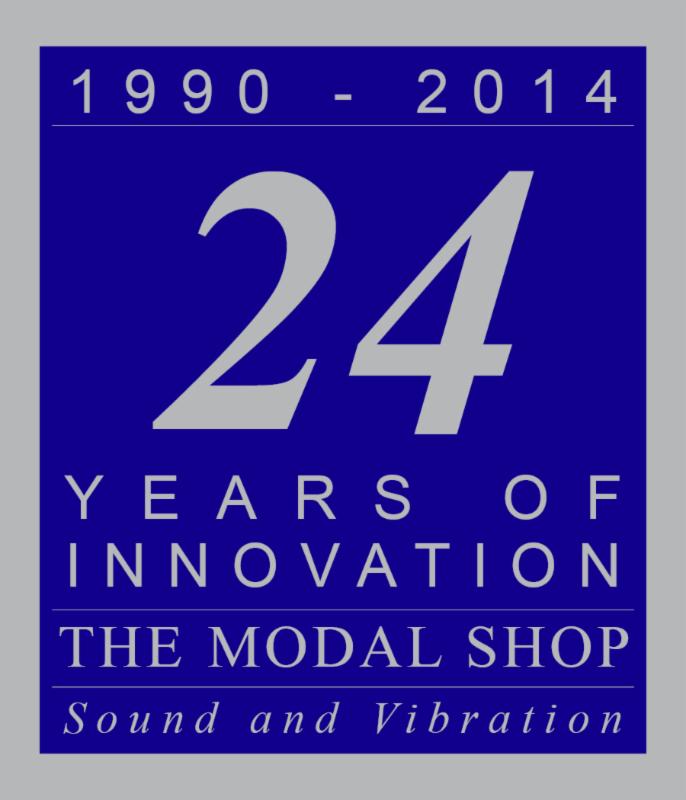 Michael J. Lally The Modal Shop, Inc.
A PCB Group Company |
|